A MEMS Piezo-Electric Energy Harvester for a Tyre Pressure Monitoring System (TPMS)
YIN, FINNEY, BHANDARY, SRINIVASAN
Summary
Piezoelectric energy harvesters have demonstrated the capability to power Tire Pressure Monitoring Systems (TPMS). We show that piezoelectric energy harvesting employed at the sub-cubic-millimeter scale can produce power output densities similar to those produced by existing cubic-centimeter scale devices. Driving device scale down, improves the ability to use bulk micro-machining techniques employed in fabrication of microelectromechanical systems (MEMS). By carefully selecting materials, geometries, and fabrication procedures we present a layered piezoelectric cantilever design that operates in the transition from flat frequency response to resonance in the range of 100-350 Hz—a band that is well matched with the expected harmonic excitations of a tire rolling on a road surface at highway speeds.

A detailed COMSOL model of our device with a resonance frequency of 899 Hz demonstrates a maximum output power of 6.6 µW/mm3 at 350 Hz. Therefore, with an array of batch micro-machined cantilevers, enough power may be generated for a modern TPMS mounted on the interior of a wheel-well.
Piezoelectrics have smaller size scales and offer a cost-effective energy harvesting solution since they can be manufactured using traditional micromachining batch processes. The accelerations experienced by a cantilever based system mounted in the wheel-well of tire are shown in Figure 1.
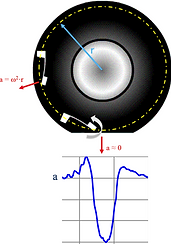
Fig 1: Radial acceleration experienced by the proof mass
For a sedan traveling at 60 mph, the acceleration of the proof mass is approximately 293g. Based on vibrational and radial acceleration data shown by Singh et al. for a pick-up truck traveling at speeds of 20-60 mph, the peak vibrations for a tire occur at various frequencies between 80 Hz and just above 500 Hz (see Figure 2).

Fig 2a: Fig 2a: Acceleration vs. time results
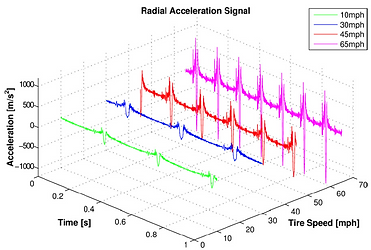
Fig 2b: Vibration Amplitudes vs. Freq.
To maximize the effectiveness of the piezoelectric material, we present a multi-layer cantilever configuration with two-layers of lead zirconium titanate 5 (PZT-5) between platinum electrodes and a silicon proof mass at the free end (see Figure 3).

Fig 3: Final packaging of the cantilever design
To avoid exceeding the yield strength of each material layer and to capture a wide band of excitation frequencies in the tire system, the layered cantilever structure is designed to operate in the transition from the bottom of the flat frequency response to resonance (see Figure 4 for range of operation from COMSOL model).
A high quality factor (Q=500) was selected to increase the magnitude of the sinusoidal frequency response at resonance (and therefore in the transition as well).
The FEA studies performed in COMSOL were primarily used to optimize the device dimensions and material selection such that:
-
(a) Power output is maximized for the smallest possible device size.
-
(b) The device does not undergo bending moments that cause high levels of principal stresses at the fixed end.
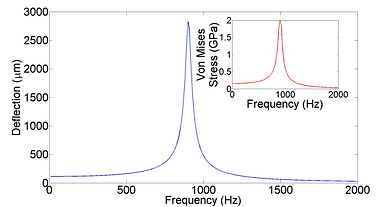
Fig 4: Displacement frequency response from COMSOL model at selected geometry, and max von mises stress in the cantilever

Fig 5: Power density frequency response in transition from flat response to resonance.
Fabrication - A number of design decisions were made to achieve a feasible fabrication process using established industry techniques, processes, and materials. One possible fabrication process that we propose is included below
In summary, our proposed design offers a viable alternative for battery powered TPMS in automobiles. We demonstrate the possibility of harnessing ambient vibration frequencies between 100 to 350 Hz using a multi-layer cantilever structure with two layers of PZT-5.
A comparison of power densities between our device and the ones reported in literature is shown in Figure 7.
It is important to note that we are operating at a device scale which is sub-mm3, and match well with power densities reported by other groups including Microgen Systems.
Microgen has a commercialized product that operates at 600 Hz with a power density of 1.25 µW/mm3. The similarity between our device performance, and that of devices in literature and those available commercially strongly motivates future device fabrication and testing.
The work we carried out was submitted in an IEEE format. We are also hoping to continue the work to explore the possibilities of publishing a paper to IEEE conference or journal.
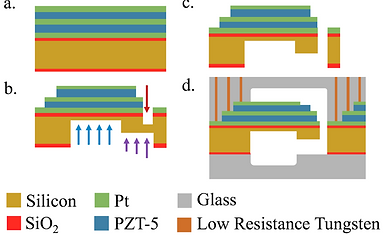

Fig 6: Fabrication process of the MEMS piezoelectric layered cantilever generator. a. Post deposition pre lift-off; b. Dry etching; c. Release d. Final Packaging
Fig 7: Comparison of device performance with literature