How Japan became the Envy of the World
An Executive summary of JIT manufacturing
After the end of the Second World War, Japan had a death toll of close to 3 million and had lost nearly a quarter of its wealth (1). However, by the 1980’s Japan was the second largest economy, just behind its World War II adversary, the United States.
There are many factors that contributed to this ‘economic takeoff’. One such factor was the burgeoning growth and productivity of the Japanese automobile sector (2). Japanese firms, led by Toyota, achieved the highest levels of manufacturing efficiency the world had ever seen, disrupting the entire automobile sector in the process. Toyota’s (JIT) technique was a radical approach to the manufacturing process and was rightly emulated and benchmarked by establishments all across the globe.
Birth
Post World War II, Toyota themselves looked to benchmark their American counterparts. But, methods like batch production and car pricing policies that were prevalent in America, were not tailored for the low demand Japanese markets (3). Reducing manufacturing costs while increasing profits was the need of the hour. Taiichi Ohno, an industrial engineer in Toyota Motor Company, sought to address the problem of inefficiencies and wastefulness that plagued his company. During his visit to America, Taiichi Ohno was influenced most by the stocking and re-stocking methods used by supermarkets. Supermarkets stock just enough product to meet consumer demand, a technique that optimizes the flow between the supermarket and the consumer (4).
This thought process of preventing over-production and eliminating wastage became core to the Toyota Way.
Features
Fig 1: Three types of Waste- Muda, Muri & Mura
The Toyota Production System sought to get rid of three types of wastage- muda, muri and mura. Muda refers to all non-value adding activities such as Transportation costs, waste from over-production, waste of motion, waste from product defects etc. The JIT philosophy centered on refining the factory layout by eliminating transporting items back and forth, thereby achieving a ‘smoother production flow’. Production was “pulled” by the demand for goods rather than being pushed by forecasted output values. This greatly reduced the inventory levels and the cost of carrying and storing goods.5
At its crux, lies the Kanban (Japanese for card), which is a system which facilitates sharing and conveying information in and between processes. The Kanban approach provided teams with a clear focus, fast output and a flexibility that made it possible to produce efficiently at low volumes.6 Moreover, it eliminated the need to stock goods between processes thus reducing the idle time of the workers as well as the machines. Another important principle of the JIT was Muri. It meant eliminating overburdening of the workers and machines by fair and equal distribution of work. This way a right pace was set so that a continuous flow is established which would not be too short as to be burdensome nor be too long to result in time wastage(7). Finally, with the Mura, irregularities in the production process were eliminated.
Shortcomings Exposed
The Kanban approach also exposed many limitations of the Ford system, with respect to employees. Kanban approach revealed how incorporating employees in the decision making process could benefit the company as a whole. Ford’s harsh attitudes to labor and low wage structures were discredited, as it would not have worked in post war Japan.
Fig 2: Automobile Costs For Comparable Cars In Japan and United States. Bain & Company study, January 1985
The key strength of the JIT philosophy is that it viewed employees as more than just muscle. Employee motivation was kept high, by promoting increased responsibility and authority. Consequently, workers perform at their best rather than being forced to do their best.(8)
Product variety was another major weakness revealed by the JIT.
“People can have the Model T in any color — so long as it’s black.” claimed Henry Ford.
The Ford system dealt with a single, non changing product. It did not cope well with multiple or new products (9).
This major weakness was overcome by the flexible Kanban approach, which was integrated to every facet of the company.
Outlook
Lean Manufacturing was an incredibly innovative method of doing business, and several companies profited by imitating these methods. Personally, I feel that imitation can, in many ways, be better than innovation.
This is evidenced by U.S based conglomerate Xerox benchmarking L.L Bean (non-competitive), in order to deal with the stiff competition Japanese manufacturers namely Canon were giving them.
The Kanban approach however, cannot be applied directly to an industry without the necessary tweaking and relevant market study as it involves company wide integration. Something, General Motors has excelled at doing. GM with its modified version of the Kanban has been able to downsize its annual inventory-related costs from $8 to $2 billion in the span of 30 years (10).
Citations
[1] — “Japanese Economic Takeoff after 1945.” Japanese Economic Takeoff after 1945. N.p., n.d. Web. 06 Oct. 2015.
[2] — Ibid
[3] — Nayab, N. “Toyota and JIT Manufacturing: The Origins of JIT.” Brighthub Project Management. Ed. Ronda Bowen. N.p., 9 May 2011. Web. 06 Oct. 2015.
[4] — “A Brief Introduction to Kanban.” Atlassian. Web.
[5] — “Taiichi Ohno.” The Economist. The Economist Newspaper, 03 July 2009. Web. 06 Oct. 2015.
[6] — Ibid
[7] — Mcmanus, Will. “Muda, Muri, Mura — Toyota Production System Guide — Toyota.” Toyota. N.p., 31 May 2013. Web. 06 Oct. 2015.
[8] — “A Brief History of Lean.” Strategos. N.p., 7 Sept. 2007. Web. 06 Oct. 2015.
[9] — Ibid
[10] — Aggarwal, Sumer C. “MRP, JIT, OPT, FMS?” Harvard Business Review. N.p., 01 Sept. 1985. Web. 06 Oct. 2015.

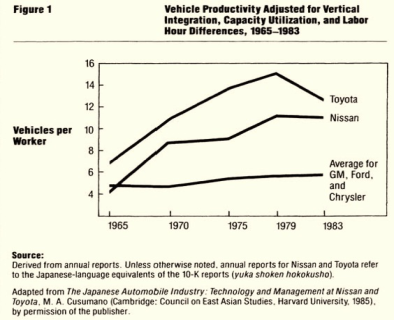
